Kuhn VB 560 OPTIFEED
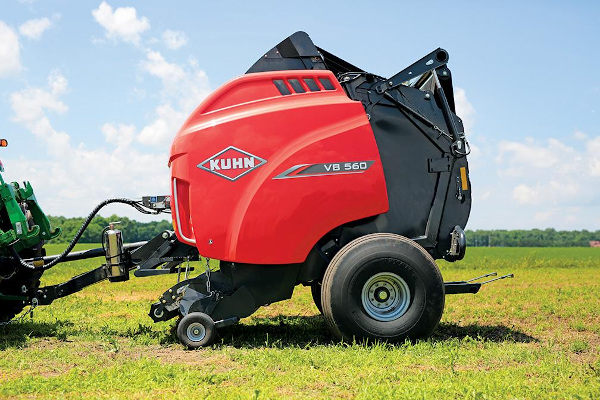
Features
INTAKE OPTIONS
Intake Options to Meet Your Operation’s Needs
Optimal Crop Pickup
The VB 560 5x6 round baler features a wide pickup with a large-diameter crop roller. The pickup is designed to maximize the full capacity of the machine. With a working width of 90 inches (230 cm), the machine is capable of working in all windrows and will not let you down, even in the toughest conditions. Heavy-duty straight pickup tines help release the crop and reduce crop wrapping. The standard crop roller compresses the crop against the pickup tines reducing friction, thus reducing leaf loss and increasing baler efficiency by evening out the windrow.
The 90” pickup features a standard pendulum frame and optional pivoting pickup wheels to allow the pickup to adapt to changing field conditions. Both fixed and pivoting pickup wheel options on this baler are semi-pneumatic to prevent punctures. Stripper bands with a unique profile on the 90” pickups, result in more aggressive and efficient pickup by exposing more of the pickup tine when needed and by pulling the crop away from the tines as it approaches the intake. A cam track pulls the tines straight down in the rearward position to avoid wrapping, making this the only hybrid pickup on the market today.
To better meet your operation's specific needs, there are three intake options available. Choose the TwinCharge direct feeding intake system, or one of our two patented Integral Rotors – the non-cutting OptiFeed rotor or the 19-knife OptiCut cutting rotor.
TwinCharge
The new TwinCharge direct intake excels in high-capacity, high-productivity needs when baling straw, dry hay, corn stalks or even soybean stubble. The TwinCharge intake, features twin feed rollers, and has an unrestricted intake unit for maximum capacity in all crop conditions. In heavier windrow conditions, such as silage or cornstalks, the top roller is acting like a pre compressor, which is powered by the primary driveline of the baler. The TwinCharge intake constantly interacts with the crop, providing high performance in loose, fluffy, or dry crops. Inline augers move the crop into the baler for positive feeding, while still allowing for max capacity thanks to the open design. This generates a huge input potential and prevents plugging of the unit resulting in a high output and minimum downtime.
Integral Rotor Technology
Available across the entire KUHN variable chamber baler range is our patented Integral Rotor Technology found on OptiFeed and OptiCut models. This simple, low-maintenance intake system guarantees an enormous throughput capacity at all times. KUHN’s integral rotor design is proven in all crops and conditions. New for the VB 560 series, is an integral rotor featuring a tri-lobe design, which allows for superior feeding. The short distance between rotor and pickup tines maintains consistent crop flow. The design of this force-fed intake makes higher forward speeds possible for increased productivity and reduces crop damage. Integral Rotors are provided with rotor tines made out of Hardox<sup® wear plates. Hardox combines extreme hardness and toughness to reduce rotor tine wear. Longer wearing life of the rotor tines will help to provide time and money savings for the operator.
Non-Cutting, OptiFeed Rotor
The OptiFeed rotor, with tri-lobe feeding tines and integrated augers, provides a consistent flow of crop into the bale chamber. The OptiFeed system easily handles a range of crops from silage to dry hay and straw. This rotor design helps even out incoming windrows for consistent bales every time.
Cutting, OptiCut Rotors
OptiCut (OC) cutting rotors are designed for unlimited intake capacity and excellent cutting quality. KUHN (OC) cutting rotors, with tri-lobe shaped rotor tines, are acknowledged by users as one of the best cutting systems on the market. The crop is guided and drawn down to the knives from an early stage which improves flow and cutting performance and also prevents unwanted plugging. The OptiCut 19-knife integral rotor system, is designed to even out the windrow and force-feed the crop into the baler for maximum throughput. The 19-knife OptiCut cutting system sizes crop down to 2.8" (70mm) in length. Each single knife is spring protected against damage from foreign objects.
BALE FORMATION
Consistent, Firm Round Bales
Fast, Perfect Bale Formation
The 6 belt, 3 roller design of the VB 560 bale chamber ensures fast, consistent bale formation whatever the intake system. Thanks to the twin tensioning arm system, the starting chamber of the baler is a triangular shape, which guarantees a direct start of the bale when the first crop enters the bale chamber. Compared to other bale chamber concepts this ensures a well-shaped core, smooth bale grow, and less power consumption. The front segment of the baler is fitted with a large crop roller and scraper that prevents crop build up at the front of the machine. The unique mix of the KUHN Progressive Density system and smart bale chamber design guarantees perfect bale formation every time.
Progressive Density – The KUHN Solution
The Progressive Density system has proven its value on all KUHN VB balers. The system increases tension as the bale grows providing a firm bale with a tough outer shell.
How Does It Work?
As the bale grows within the bale chamber, the belt tensioning arm is subjected to steadily increasing resistance from two hydraulic cylinders and a spring tensioner. So as the diameter increases, the bale’s density does too. The result is a very firm bale with a moderate core – not too soft, not too hard. With a tougher outer layer, straw bales will be more tolerant to bad weather conditions, while silage bales will maintain their shape for improved stacking and easier handling.
Twin Tensioning Arm System
Twin tensioning arms provide higher density from improved belt tension control and response time.
Tension arm 1 provides the bale shape. This tension arm is continuously distributing the tension of the belts around the bale keeping the density consistent in the bale as more crop is added.
Tension arm 2 is mounted in the tailgate of the baler and creates the high belt tension that will be distributed by tension arm one. When opening and closing the tailgate of the VB 560, tension arm 2 will tension the belts quickly keeping them aligned so the driver can continue with baling. This results in an opening and closing time of only 4 seconds!
Fast Tailgate
The KUHN VB 560 features the fastest tailgate operation on the market thanks to the twin tensioning arm system. Within 4 seconds the bale is ejected and the tailgate is closed again!
NET WRAP & ELECTRONICS
KUHN Net Wrap & Electronics"
Net Wrap System
One of the final steps in creating the perfect bale is the wrap. Securing a bale to protect it from the elements and from losing its shape is one of the most crucial steps. The less time required to secure the bale, the higher the baling operation output. KUHN’s net wrap system guarantees reliable and secure wrapping. The net wrap, with active stretch technology, ensures a firm bale shape with constant net tension throughout the entire wrapping cycle. KUHN’s innovative design maintains constant net tension during the wrap process. The net wrap system runs at 90% of the bale’s rotational speed to be able to stretch the net without breaking it. After leaving the bale chamber, the bale will not expand and therefore it will hold its density. The net wrap system spreads the net to the corners of the bale to prevent air pockets once the bale is wrapped, which will preserve the forage quality for longer.
Easy-To-Load Front Net System
The net is fed into the front of the bale chamber to ensure it is taken by the bale immediately and provides great visibility during operation. The VB 560 provides storage for up to two spare rolls of net wrap, one on each side of the machine. Due to the innovative net loading brackets, only one side of the net roll needs to be lifted when easily sliding the net roll into the active position. This KUHN side-load system allows the operator to take a roll of net wrap from the storage position to the active position while only supporting a fraction of the rolls weight, allowing for greater efficiency and operator comfort.
Productivity at Your Fingertips
The key to achieving the productivity you expect from your KUHN machine, is the user interface. We listened carefully to the users of our machines to develop our new interfaces and monitors. The objective is to have a clear view of what your machine is doing at any time and to have all important settings at your fingertips. This ensures that you have full control of your machine.
KUHN VB 560 balers are ISOBUS compatible with an intuitive user interface, easy to control via the ISOBUS terminal of the tractor or via KUHN’s CCI 50, CCI 800 or CCI 1200 terminals. You can easily change settings such as bale density or net wrap layers from the comfort of your tractor seat.
Specifications
BALE DIMENSIONS | VB 560 OPTIFEED |
Bale diameter | 31.5" - 72.8" (80 -185 cm) |
Bale size - width x diameter | 5' x 6' (1.56 m x 1.85 m) |
Bale width | 61.5" (156 cm) |
BALE CHAMBER | |
Bale chamber | 1 starter roller - 2 bale chamber rollers - 6 endless belts |
Bale chamber idler rollers | Standard with HD bearings and seals |
Bale pressure | 290 - 2393 psi (20 - 165 bar) |
Teardrop bar for bale chamber | Standard |
Proportional valve soft core | Standard |
Belts | 6 endless belts standard |
INTAKE | |
Chain lubrication system | Optional |
Intake system | Integral rotor with Hardox tines |
Number of knives | - |
Drop floor | - |
Minimum cutting length | - |
Knife protection system | - |
Pickup width | 90.6" (230 cm) |
Number of pickup tine bars | 5 |
Pickup gauge wheels | Standard fixed wheel with semi-pneumatic tire |
Pickup windguard | Standard with large 8.5" (217 mm) diameter roller |
MACHINE CHARACTERISTICS | |
Bale kicker | Standard |
Bale packaging system | Net wrap only |
PTO power requirement | 120 hp (88 kW) |
PTO speed | 1,000 standard, 540 optional |
Overload protection | Cam clutch |
Drawbar hitch | Standard height adjustable, upper and lower attachment possibilities |
Tires | 21.5L x 16.1 standard, 14.1 x 16.1 optional |
Transport width | 120" (305 cm) on 14L X 16.1 wheels, 126" (320 cm) on 21.5L X 16.1 wheels |
ISOBUS Electronic monitor | No terminal standard, CCI 50, CCI 800 or CCI 1200 control box optional |
Road lights and signaling | Standard |
Required tractor hydraulic connections | 1 double acting valve, 1 open return, 1 single acting |
MACHINE WEIGHT | |
Minimum machine weight | 9,590 lbs (4,350 kg) |